Birth of a Filigree piece: Learn about the process
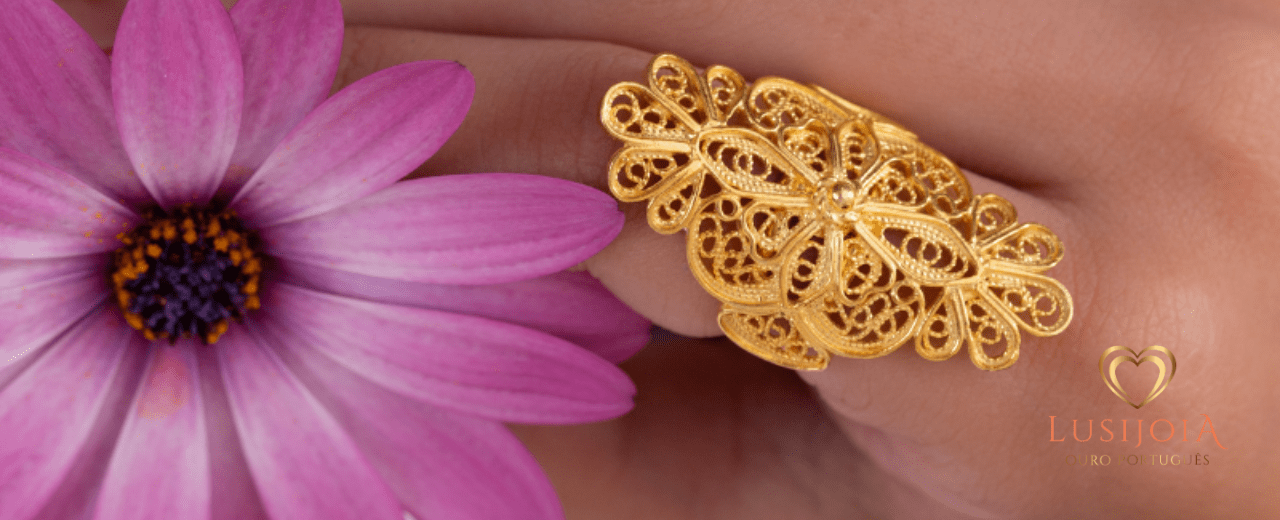
Filigree is one of the oldest and most refined jewelry techniques, dating back thousands of years and is practiced in various cultures all over the world. In Portugal, filigree gained a special place, standing out for its delicacy, complexity and beauty. The process of creating a filigree piece is a true art, requiring skill, patience and extraordinary dedication. Let's explore the steps that transform simple metal strands into stunning jewelry?
Material Selection
It all starts with choosing the material. Filigree pieces are usually made from precious metals, such as gold or silver. In Portugal, 925 sterling silver and 19.2 carat gold are widely used in this art. These metals are chosen for their malleability and their ability to maintain their shape after being worked into fine threads.
Fusion and Lamination
The chosen metal is heated until it becomes liquid and then poured into molds to form bars or ingots. These bars are then passed through rolling mills to be reduced into thin sheets. The process continues with stretching these sheets until they become very thin wires, often less than a millimeter thick. The metal (gold or silver) is placed in the crucible which is heated in the forge at a temperature of around 900 degrees centigrade until it melts. The crucible is then removed with tongs and the metal poured into an iron ridge that gives it the shape of a long bar. The sheet thus obtained is then hammered and drawn until it becomes a sheet. The model is passed from the drawing to this sheet, and the sheet is subsequently cut or sawed.
Yarn Creation
Threads are the soul of filigree. They are created from rolled sheets, which are stretched and rolled until they reach the desired thinness. These strands are then twisted into pairs, a procedure that gives them the necessary resistance for the next step. The wire obtained by casting and casting in a wire machine is beaten on the anvil, and the first reduction in thickness is carried out on the drawing machine. After achieving the desired size, it is formed on the die or damask and, finally, it is stretched on the so-called rubies - tool pieces that are wider than the die - which allow obtaining threads with thicknesses of less than 0.2mm.
Design and Structure
Before starting to assemble the piece, the goldsmith designs the filigree pattern. These designs are often inspired by traditional motifs such as hearts, flowers and spirals. The structure of the piece is made with thicker threads, which form the base on which the fine threads will later be applied. The drawing must be precise and clear and provide all the data necessary for correct reading and transposition into metal. They can be free, intuitive drawings, the result of the artisan's observation and reproduction, or simple drawings without taking into account more complex and complete issues that technical drawing imposes. The drawing must follow a scale that is as realistic as possible, to avoid errors in transposition onto the part, through incorrect interpretations and projections that compromise the perfect representation of the drawn part. Currently, in some goldsmith workshops and designers who design more contemporary pieces, methods are being transformed and gradually computerized. However, for more traditional pieces, “old” debuxos religiously kept by the goldsmith are used (or, not infrequently) images kept in the memory of older goldsmiths. Therefore, the starting point for creating a filigree piece begins with the drawing, generally made on a sheet of paper by the artisan himself or selected by him from a panoply of pre-existing drawings well kept in traditional workshops.
Assembly and Welding
The assembly stage is one of the most delicate. The thin wires are cut and shaped to fit perfectly into the spaces in the main structure. This work requires extreme precision and a keen eye for detail. Once the wires are in place, they are secured with small solder points, which are applied with a fine flame. This welding must be done very carefully so as not to melt the delicate wires. The process consists of wetting the part in water or a type of gum and pouring solder onto the part (using rubber). It is a difficult operation and requires a lot of experience and expertise to be carried out well. The craftsman welds with a torch and the ultimate objective of this task is to combine the different components of the piece without the welding being visible.
Finishing, Cleaning and Polishing
After welding, the part is then immersed in chemical solutions to remove any welding residue and impurities. This cleaning process is crucial to ensure that the piece maintains its shine and purity. The piece is then manually polished to obtain a perfect finish. Polishing highlights the intrinsic beauty of the metal and gives the piece its characteristic shine. It should be noted that the filigree pieces, after being welded, become oxidized and dirty, having to be annealed again. To do this, several pieces are placed in a container that is heated in the forge at high temperatures. After cooling, the pieces are then bathed in a solution of water with boiling sulfuric acid, 3 or 4 times, until they take on the color of silver. The piece is then rubbed with a very fine metal brush with water and detergent, until it becomes shiny, or it is polished using a ball machine or magnetic polishing machine. Finally, the piece goes to the dryer where it will be dried.
Quality Check
Before being considered ready, each piece undergoes a rigorous quality check. The goldsmith carefully examines the jewelry to ensure there are no flaws or imperfections. This step is crucial to ensure that each filigree piece maintains the high quality standards for which Portuguese jewelry is known and recognized worldwide.
Commercialization
Finally, after all previous steps have been completed, the pieces are ready to be sold.
Filigree jewelry is often presented in specialized stores such as goldsmiths, craft fairs and jewelry exhibitions. Each piece is a unique work of art, carrying with it the tradition and skill of generations of artisans.
At Lusijoia, we have a wide range of Portuguese Filigree Jewelry, from anéis, colares, pulseiras, brincos, etc.
Conclusion
The process of creating a filigree piece is a complex and fascinating journey, combining ancient techniques with the art and passion of traditional goldsmiths. Every step, from material selection to quality checking, is carried out with meticulous care. This painstaking craftsmanship results in jewelry that is immensely beautiful, but also represents Portugal's rich cultural heritage. Knowing this process allows us to appreciate even more the value and beauty of filigree pieces, true works of art that transcend time.
Don't you agree?